At present, there are two kinds of production processes for bamboo yarn used in hand tufted carpet, hand made carpet and robot tufted carpet. They are made by viscose method and new solvent method.During the dipping process, the cellulose combines with NaOH to even generate sodium alkoxide, which also swells and the degree of polymerization is reduced. The concentration of dipping lye is 18%-20%, the dipping time is 45-60 minutes, and the temperature is about 20 ℃. The pressing and crushing are carried out in a combined machine. The pressing is to remove excess lye to facilitate the yellowing reaction. Smooth progress, because too much lye will consume CS2, and a variety of side reactions will occur. Crushing is to pulverize the very dense alkali cellulose after squeezing into fine loose crumbs, increase the surface area, and facilitate subsequent Each step of the reaction can proceed more evenly.
Artificial Cotton Filament Viscose Yarn 305/3TEX
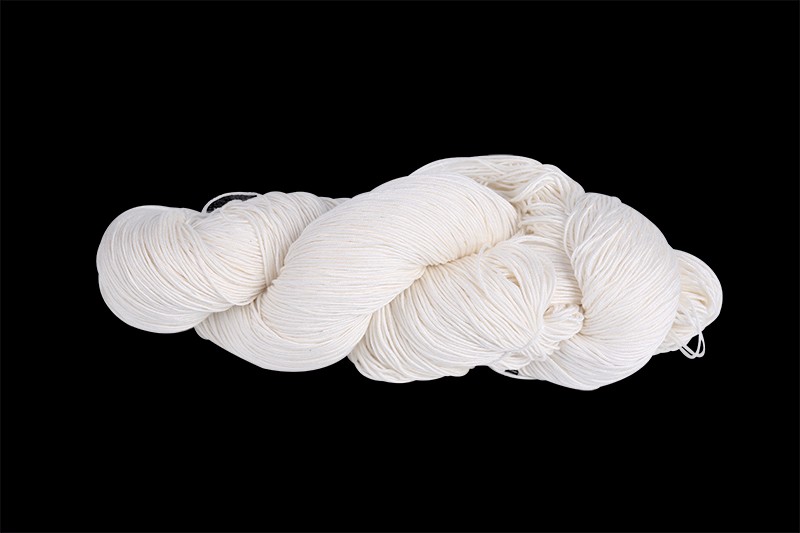
Artificial Cotton Filament Viscose Yarn 305/3TEX
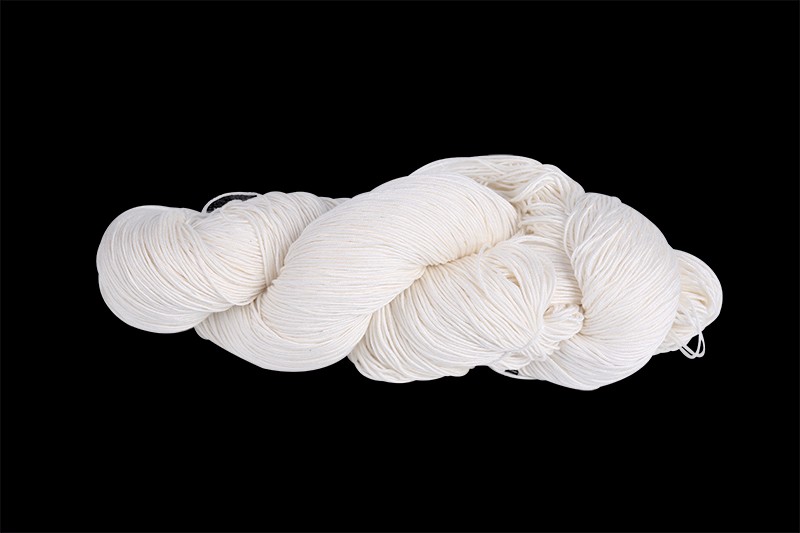
Name:Artificial Cotton Filament Viscose Yarn 305/3TEX
Specification: 350/6TEX
Introduction: It is made by 100% viscose short fiber, high quality & competitive price mainly used for mainly used for a series of handmade Carpet, Tapestry, Craft carpet Ect.
Laocheng is carried out in an old box, which is a closed workshop with heating devices, conveyor belts, etc. The old achievement is to use the oxidation of air to break the chain of the alkali cellulose molecule, reduce the degree of polymerization, and decrease the viscosity. The key to aging is to control the temperature and time of the aging. Generally, low temperature and long time are used instead of high temperature, because the temperature is too high and the cracking is intense. It is easy to make the polymerization too low and the molecular weight distribution is uneven.
Yellowing is to make alkali cellulose react with CS2 to generate sodium cellulose yellow, which can be dissolved in NaOH solution to form spinning solution. Yellowing reaction is mainly a gas-solid phase reaction, and the reaction process includes CS2 vapor according to the diffusion mechanism The process of permeating from the surface of the alkali cellulose to the inside, and the process of reacting the infiltrated part of CS2 with the hydroxyl groups on the alkali cellulose. The yellowing reaction is a reversible reaction and mainly depends on the concentration of caustic soda and carbon disulfide.
The dissolution process of cellulose xanthate is carried out in a dissolving kettle with stirring. The massively dispersed cellulose xanthate is pulverized into fine particles gradually after continuous stirring and circular grinding. After the dissolution, in order to minimize the quality difference between the batches of viscose, it is necessary to mix the batches of viscose that have been dissolved to make the viscose uniform and easy to spin.
A series of chemical and physicochemical changes that occur during the placement of viscose is called the maturation of viscose. The maturity of the viscose refers to the degree of stability of the viscose to the coagulation effect. It is generally expressed by the degree of stability of the viscose in the NH4Cl solution. The maturity is one of the important indicators of viscose, it directly affects the performance of the finished fiber of the spinning forming process. At the beginning of maturation, the viscosity drops sharply, and as maturation continues, the viscosity begins to rise again, even forming viscose particles.
Filtration is to remove the particles in the viscose solution to prevent the spinning hole from blocking the spinneret during the spinning process, causing the filament to break, or forming a weak link in the finished fiber structure, which is the decrease of fiber strength. It usually passes through three filtrations, the filter medium is flannel and fine cloth.
Carding: Strengthen the carding effect of bamboo fiber to prevent neps. The licker rollers, cylinders, cover plates, and doffer clothings should be sharp, and the spacing of cylinder cover plates can refer to the glue gap. If the gauge is too small, the fibers will be broken during the carding process; if the gauge is too large, the fibers will twist and form neps during the carding and transfer process. The speed and tension of the various parts should be relatively small.
Drawing: The strength of bamboo fiber is low, and the speed is low. The number of combined roots is adjusted according to the blending ratio. The tampon road should be smooth and clean, and the automatic stop should be sensitive. This process has higher requirements for temperature and humidity. The best temperature is around 25℃ and the humidity is around 70%. During the small test, because the humidity was too low to meet the requirements, the drafted beard was wrapped around the front roller due to static electricity, affecting life. After treatment to increase humidity, it passed smoothly
Spinning: The surface of the bamboo fiber is smooth, and the cohesion between the fibers is poor. When selecting the twist coefficient, it should be too large, provided that it affects the draft of the spun yarn. Spindle speed selection is lower than when spinning polyester/cotton products. All channels should be smooth and clean. The false twister has no burrs. The requirements for temperature and humidity are the same as the drawing process.